Purging, Piping, and Safety
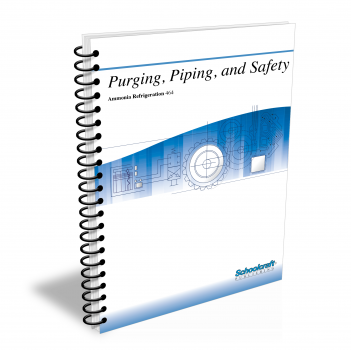
Course Number: 464
The Purging, Piping, and Safety textbook explains the effects of noncondensables on an ammonia system and the importance of their removal. It covers a wide range of piping considerations—sizing, flow rate, pressure drop, and others. It concludes with a thorough coverage of safety codes and programs, including ANSI/ASHRAE, IIAR, OSHA, and EPA information.
Does your curriculum require additional topics not included in this textbook? Build a customized version of the Purging, Piping, and Safety textbook below.
Recommended Contact Hours – 10
Preview a Chapter
Available Supporting Material
- Table of Contents
- Exam Copies
- Suggested Titles
Table of Contents
Chapter 1: Purging Air and Noncondensables
Topics: Materials to be purged; Effects of noncondensables; Power penalty; Purge point locations; Automatic purging; Economics of purging
Learning Objectives:
- List common noncondensable vapors and discuss their effects in a refrigeration system.
- Discuss the power penalty resulting from noncondensable gases in terms of compression and loss of refrigeration capacity.
- Explain how to determine the presence of noncondensables.
- Explain how to minimize the entrance of noncondensables and describe common entry points.
- Compare the features and operation of manual and automatic purging equipment and name the best connection points for the purge unit.
- Discuss the economic benefits of the purge unit in terms of typical payback times.
Chapter 2: Ammonia System Piping
Topics: Pressure drop in pipes; Laminar and turbulent flow; Line sizing, flow rate, suction line pressure drop, discharge line pressure charts; Special piping situations
Learning Objectives:
- Discuss the relationship between pressure drop requirements and pipe sizing.
- Discuss the factors that affect the pressure drop in a pipe.
- Explain the significance of the Reynolds number and the distinction between laminar and turbulent flow.
- Discuss the use of various kinds of line sizing charts including flow rate tables, equivalence tables for fittings and valves, and pressure drop charts.
- Explain how to select the proper suction line, discharge line, and liquid line sizing for an ammonia system.
- Discuss special piping situations that require alternative sizing or installation.
Chapter 3: Ammonia System Safety Codes and Guidelines
Topics: Codes for ammonia refrigeration systems; ANSI/ASHRAE 15-1994; ASMEB 31.5; IIAR2; IIAR bulletin 111; IIAR bulletin 112
Learning Objectives:
- Describe the basic differences between ASHRAE and ASME codes and IIAR standards and guidelines.
- Discuss several main points in the ASHRAE 15-1994 safety code for mechanical refrigeration.
- Describe code requirements based on the occupancy classifications, leak probability classifications, and refrigerant characteristic classifications.
- Describe several requirements in the ASME B 31.5 refrigeration piping code concerning the materials and fabrication of refrigeration piping systems.
- Name several safety requirements specified by IIAR 2 for ammonia refrigeration equipment.
- Describe the kinds of information provided by IIAR bulletins.
Chapter 4: OSHA Process Safety Management
Topics: OSHA regulations; PSM requirements; Estimation of ammonia inventory; PSM plan development; Process safety information, hazard analysis; Standard operating procedures; Contractor procedures
Learning Objectives:
- Discuss the purposes of Process Safety Management and describe the thirteen elements that make up PSM.
- Describe the process for estimating a plant's ammonia inventory and establishing a plant ammonia library and explain why each is needed.
- Discuss the personnel and steps involved in developing a PSM plan for a specific refrigeration plant.
- Describe the process hazard analysis (PHA) and explain how it can reduce the likelihood of ammonia accidents and spills.
- Describe the requirements for preparing standard operating procedures (SOPs) for all normal plant service, repair, and maintenance.
- Discuss contractor responsibilities for PSM.
- Discuss the importance of management-of-change procedures in keeping paperwork up to date.
Chapter 5: EPA Regulations and Ammonia Safety
Topics: 40 CFR 68; Worst case/alternate ammonia release scenario; Elements in common with OSHA PSM; Penalties for nonconformance
Learning Objectives:
- Describe the purposes of the EPA Risk Management Plan and compare it to the OSHA Process Safety Management program.
- Explain the reasoning behind the dual hazard assessment requirements of a worst-case ammonia release and the more practical alternative ammonia release.
- Discuss the toxic end point criteria for an ammonia release and distinguish between rural and urban end points and differences in requirements.
- Discuss the importance and difficulties of presenting the required release data and plan to the community.
- Discuss the hazards of working with ammonia and the importance of using personal protective equipment to avoid or minimize the effects of an ammonia release.
- Describe correct first aid procedures pertaining to contact with ammonia vapor and liquid.
Request Exam Copies
Exam Copies
Ready to see a copy of our textbooks? After selecting which textbooks you’d like to review for your course, you can submit your request by either logging in or creating an account so we know where to ship your exam copies. A representative from Schoolcraft will contact you to confirm and finish processing your request.
Exam copies are always free and yours to keep.
Selected Exam Copies
none selected
* Maximum of five copies can be ordered