Introduction to Robotics
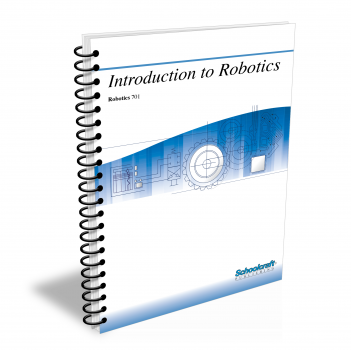
Course Number: 701
The Introduction to Robotics textbook offers a basic survey of what robots do, how they operate, and how they are integrated into automated manufacturing. It explains robotic terminology, the classification of robots, and their principles of operation. It traces the interaction of sensors and machines in a robotic work cell, and concludes with a look at programming and "teaching" methods.
Does your curriculum require additional topics not included in this textbook? Build a customized version of the Introduction to Robotics textbook below.
Recommended Contact Hours – 11
Preview a Chapter
Available Supporting Material
- Table of Contents
- Exam Copies
- Suggested Titles
Table of Contents
Chapter 1: Robotics in Automated Manufacturing
Topics: Evolution of Robotics; What is an Industrial Robot?; Essential Characteristics; Robots and Automated Manufacturing; Project Manufacturing; Job Shop; Batch Manufacturing; Repetitive (Flow) Manufacturing; Continuous Manufacturing; Robot Safety
Learning Objectives:
- Identify why robots did not appear in large numbers in manufacturing until the late 1970s.
- State the Robot Industries Association's definition of an industrial robot and explain the two key words.
- Describe how industrial robots are used in batch production systems.
- Explain how industrial robots are used in repetitive manufacturing systems that utilize transfer lines.
- List at least three factors that should be considered as part of a risk assessment when a robot system is in the development stage.
- Describe and contrast the following guarding methods: barrier, presence-sensing device, awareness device, warning system.
- Define the term zero-energy state.
Chapter 2: The Basic Robot System
Topics: Manufacturing and Robot Systems; Robot Arm; Robot Controller; Power Source; Tooling; Teaching/Programming Device; Data Storage; Definition of Terms; Critical Specifications; Payload; Degrees of Freedom; Drive Power; Repeatability; Accuracy; Work Envelope Dimensions; Speed; Memory Capacity; Programming Support; End-of-Arm Tooling; Environmental Requirements
Learning Objectives:
- Name and describe the basic building blocks of an industrial robot.
- Name and describe the additional components that make up a robot system.
- Define the following robot terms: degrees of freedom, position axes, orientation axes, work envelope, tool center point.
- Define and give an example of the following specifications for industrial robots: payload, repeatability, memory capacity, and environmental requirements.
- Explain the difference between accuracy and repeatability in robots.
Chapter 3: Robot Classification I
Topics: Robot Classification; Classification by Control System; Open-Loop Control; Nonservo Operation; Advantages of Open-Loop Control; Disadvantages of Open-Loop Control; Applications for Open-Loop Control; Closed-Loop Control; Advantages of Closed-Loop Control; Disadvantages of Closed-Loop Control; Applications for Closed-Loop Control; Classification by Application
Learning Objectives:
- Identify the five methods of classifying industrial robots.
- Explain the difference between robots with closed-loop control and those with open-loop control.
- Describe the techniques used in closed- and open-loop control in robot systems.
- List the advantages and disadvantages of open- and closed-loop control in robot systems.
- Distinguish between assembly and nonassembly robots according to the application for which they were designed.
Chapter 4: Robot Classification II
Topics: Classification by Arm Geometry; Cartesian (Rectangular) Arm Geometry; Cylindrical Arm Geometry; Spherical (Polar) Arm Geometry; Articulated Arm Geometry; Classification by Power Source; Classification by Path Control; Classification by Intelligence Level
Learning Objectives:
- Classify robots by arm geometry, power source, and path control techniques.
- dentify the basic robot work envelopes and name the arm geometries that produce them.
- Name the basic power sources used for robot motion and give an advantage and disadvantage of each.
- Identify the basic path-control techniques and describe their characteristics.
Chapter 5: Work-Cell Sensors
Topics: Sensor Overview; Simple Contact Sensors; Simple Noncontact Sensors; Simple Process Control Sensors; Complex Sensors; Complex Sensor Interface; Complex Contact Sensors; Complex Noncontact Sensors; Complex Process Control Sensors
Learning Objectives:
- List the two types of interfaces and three groups of sensors used in industrial robot systems.
- Describe the primary simple contact sensor commonly found in robot systems.
- Identify and explain the operation of the two simple noncontact sensors most often used in industrial robot installations.
- Explain the difference between the simple sensor interface and complex sensor interface.
- Identify and describe vision and tactile sensors and the systems required to support them.
Chapter 6: End-of-Arm Tooling
Topics: General Requirements; Tooling Terms; Tooling Power Sources; Tooling Overview; Standard Grippers; Servo or Nonservo Grippers; Vacuum Devices; Magnetic Devices; Flexible Pneumatic Devices; Special-Purpose Tooling; Protecting End-of-Arm Tooling; Compliance
Learning Objectives:
- Name the five general requirements all tooling must satisfy.
- Identify and describe briefly the four basic tooling power sources.
- Describe the five categories of end-of-arm tooling used in robot applications.
- Explain the function and advantages of a quick-change device.
- Define the term compliance and explain why it is important.
Chapter 7: Robot Teaching and Programming
Topics: Work-Cell Programming; Controller Functions; Robot Programming; On-Line Programming; On-Line Programming Example; Off-Line Programming; Defining Programmed Points; Writing Program Statements; Work Cell Control with a PLC; PLC Programming Example
Learning Objectives:
- List and describe the four basic functions of the computer(s) controlling an automated work cell.
- Name the two major types of robot programming and give advantages and disadvantages of each.
- Name and describe two basic methods of teach programming and tell when each is used.
- List three advantages of off-line programming.
- Name the two elements of a computer program for off-line robot programming.
- Explain the basics of ladder logic programming.
Request Exam Copies
Exam Copies
Ready to see a copy of our textbooks? After selecting which textbooks you’d like to review for your course, you can submit your request by either logging in or creating an account so we know where to ship your exam copies. A representative from Schoolcraft will contact you to confirm and finish processing your request.
Exam copies are always free and yours to keep.
Selected Exam Copies
none selected
* Maximum of five copies can be ordered